Replacing the Rear Wheel Bearings
on the 1985 300D (W123)
by dmorrison
12/1/07
This DIY is applicable to the W123 and W126.
My son's new 85 300D had the rear left wheel hub loose and required replacing. I was quoted $400-435 from 2 independent shops and $775 from the dealer. I wanted to learn how to do this job (35-130) The MB service manual calls for 11 specialty tools to complete this job. I had a good conversation with the old Mercedes specialist at the dealer and asked what "specialty" tools are really required. He said Just the Special castle socket . MB 115 589 02 07 00.
All the races can be removed and installed with conventional tool. So here is the write up of the job. The most difficult task was removing the outer bearing/race assembly off the hub. I destroyed the bearing holder and totaled the race. I would suggest bring the hub to an independent or the dealer and pay a few bucks to have then do this. They should not charge much. I figure $25-30. If it's over $50 I would do it myself. I did not get a price for doing it.
Tools and parts needed for the job on a 1985 300D
- 1/2 inch drive ratchet.
- Special socket. MB tool 115 589 02 07 00
- Brass drift.
- Hammer
- Dead blow hammer
- 3 jaw puller
- Large flat washer or plate ( used with the 3 jaw puller over the hub opening)
- Dial gauge, Metric preferred, SAE OK ( it's what I have)
- Large flat screwdriver
- Flat chisels, 2 small, 2 large
- Dial gauge base holder
- Wheel bearing kit Mercedes part number 123 350 00 68 ( 1985 300D)
- Mercedes wheel grease Mercedes part number 002 989 51 10
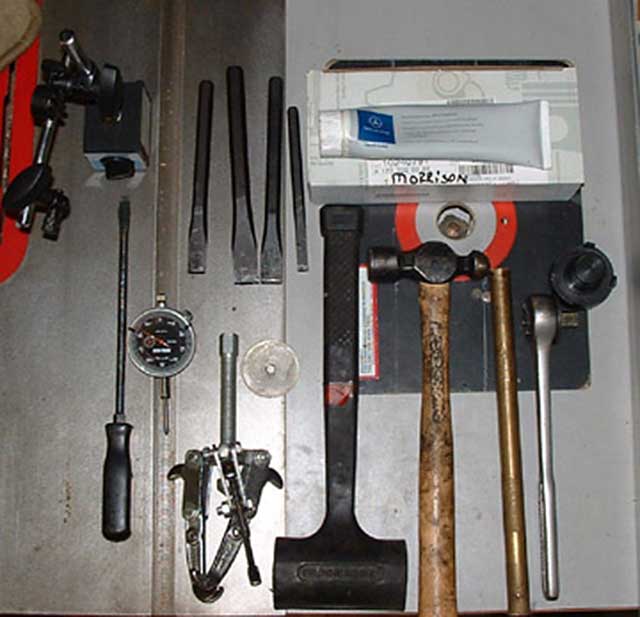
Remove the center bolt holding the axle to the hub. You may have to use the brass drift to remove the axle.
Unbolt the caliper.
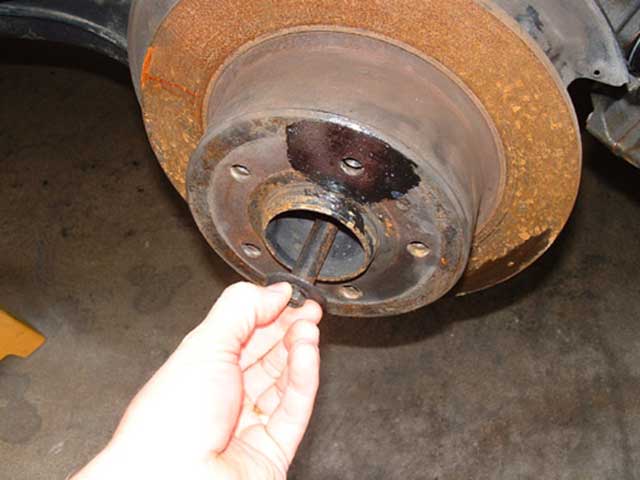
Hang the axle and caliper with wire , out of the way. Do not
Allow the caliper to hang on its rubber hose. Do not allow the axle to drop.
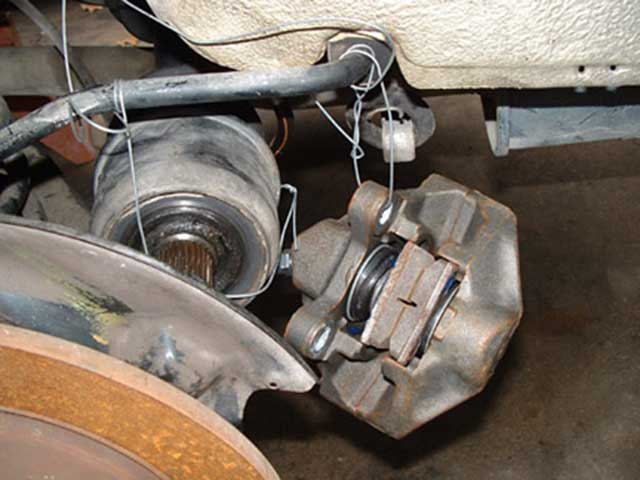
Remove the rotor. Parking brake must be released to remove the rotor.
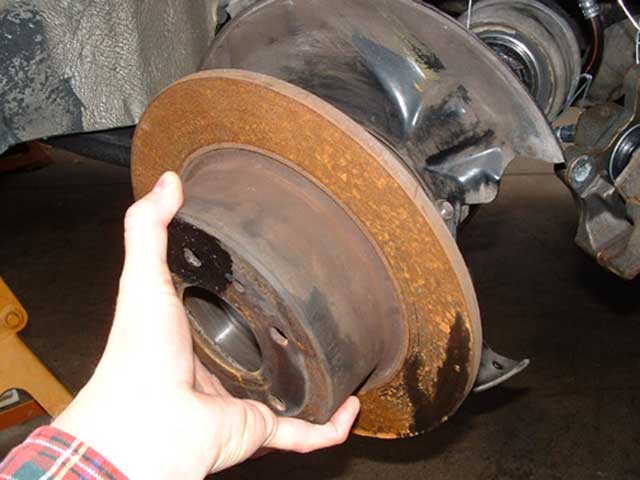
The slotted nut and inner bearings.
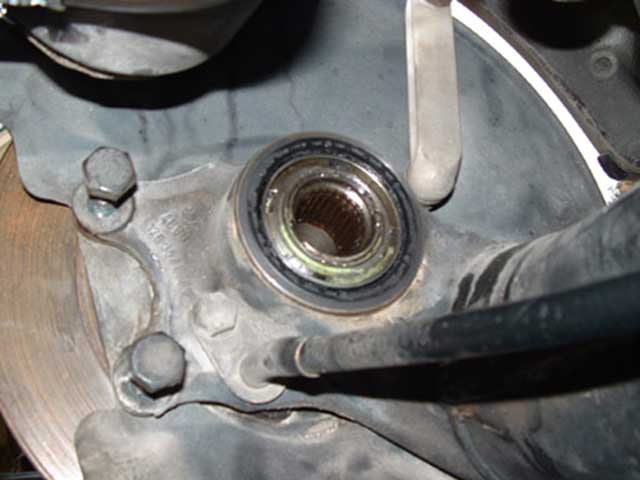
Purchase 2 lug bolts or 2 bolts to be sacrificial bolts for the job. M12 X 1.5 . Install them as shown
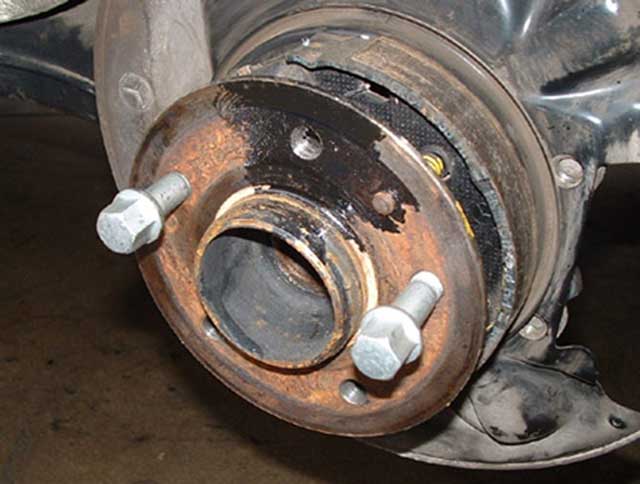
The "special" tool needed for this job on a ½" drive ratchet.
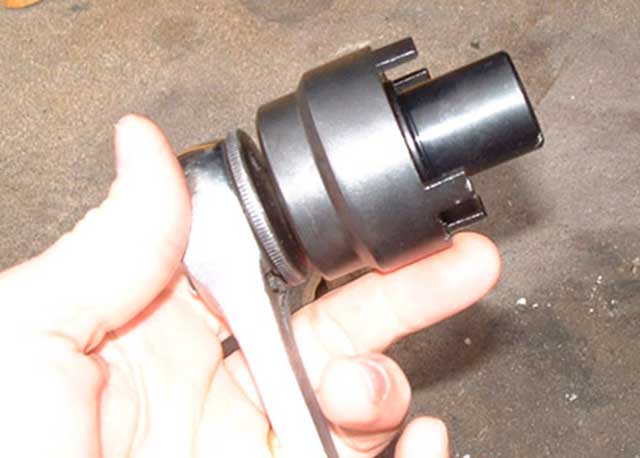
I used a black pipe clamp since I have a wood shop. Any strong and long ( about 4 foot long ) bar will do. The setup shown will allow you to loosen the slotted nut.
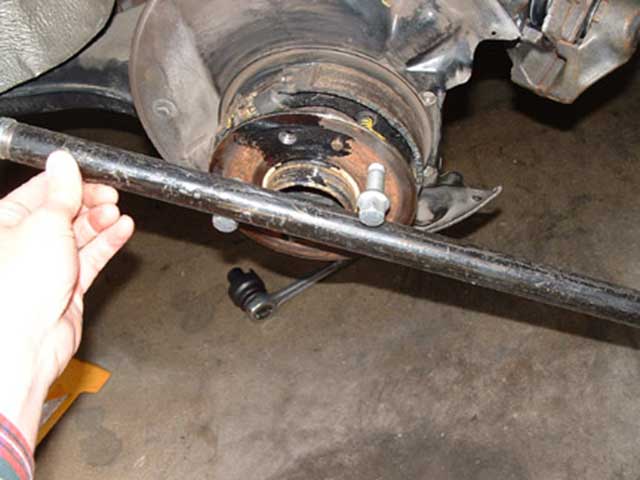
Install the socket and ratchet as shown. This will allow you to loosen the nut on the outside with the back pipe.
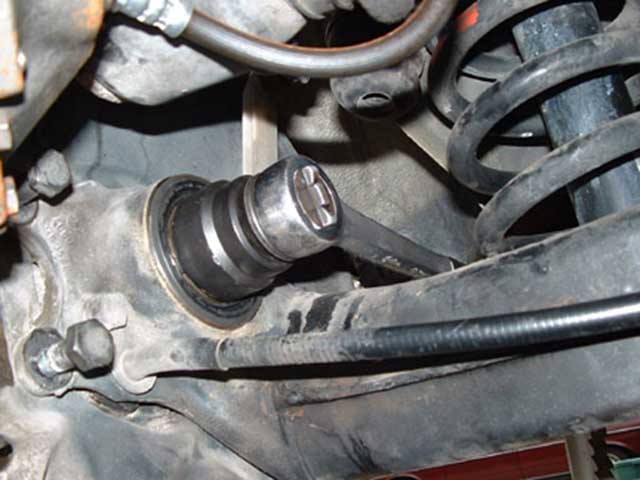
Using the black pipe I loosened the slot nut.
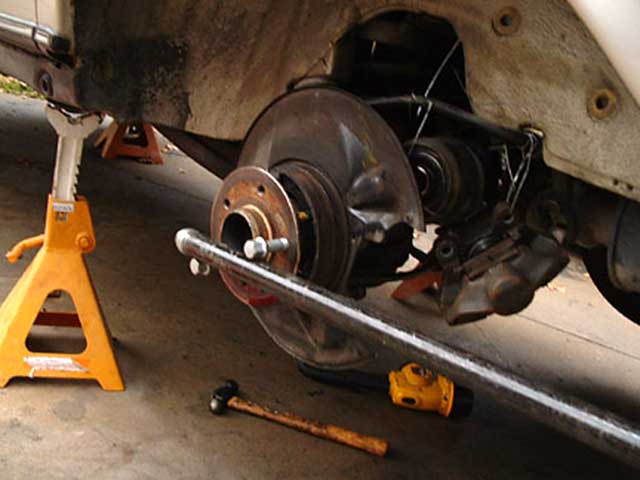
Remove the seal on the inside of the hub from underneath the car. I used a large screwdriver.
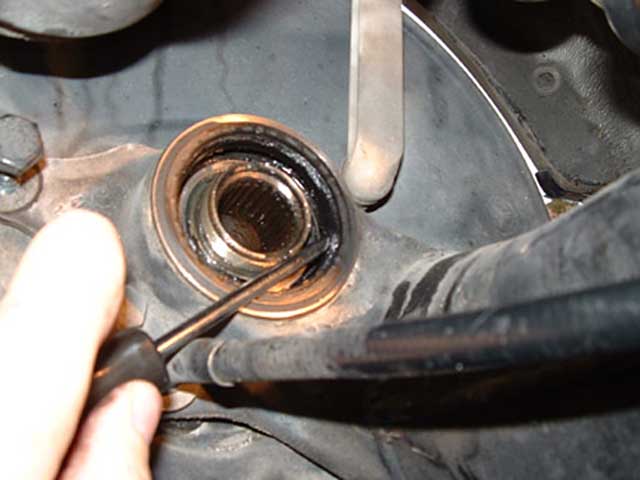
I did not have a slide hammer to remove the hub. I did the
Following, I Used a brass drift to hammer out the hub from under the car. I hammered it out about ½ inch. I then installed the rotor as shown and used it as a slide hammer to get the hub to release from the inner bearings.
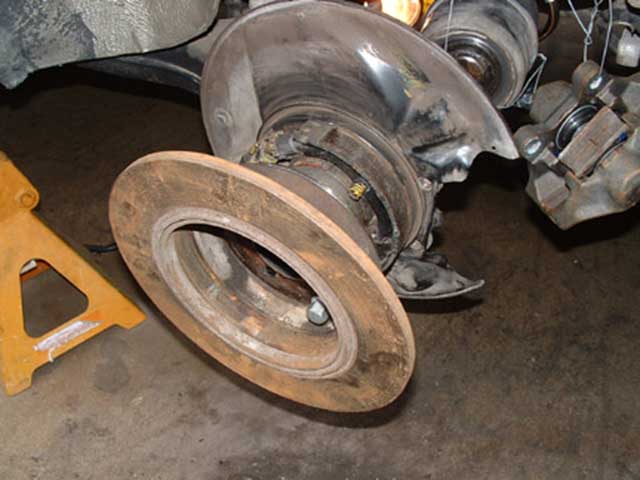
This is the hub removed and attached to the rotor.
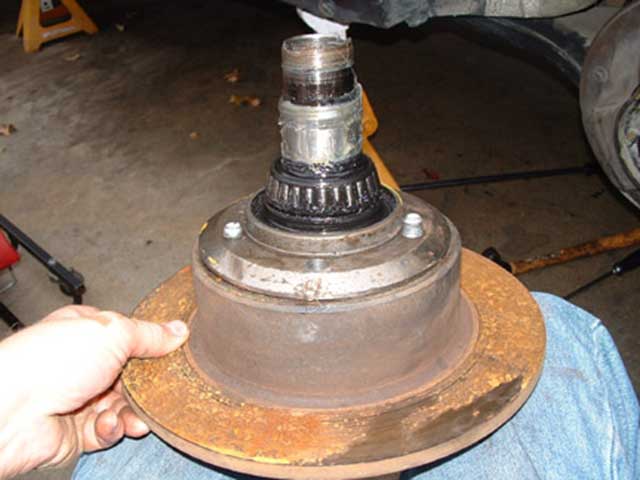
Now for the most difficult part, removing the outer bearings and race assembly. As you can see I destroyed the bearing cage in the process and tore up the inner race.
To do the job Use a wide flat chisel and force it between he inner race and the hub. ( I forgot to mark the picture, page 8 of the post has a photo of where to force the chisel ). As the race starts to separate from the seat you can use a 3 jaw puller
And a flat washer to pull the bearings/race assembly off the hub.
If you try to pound away at the bearing cage it will come apart, as shown. Then if you try and chisel at the lip that is left. It will break apart and fly everywhere ( wear safety glasses ).
So the solution is to use the flat chisel between the race and the hub shoulder.
Another suggestion would be to bring the hub and new bearings to an indy or the dealer and pay them a few bucks to do this part.
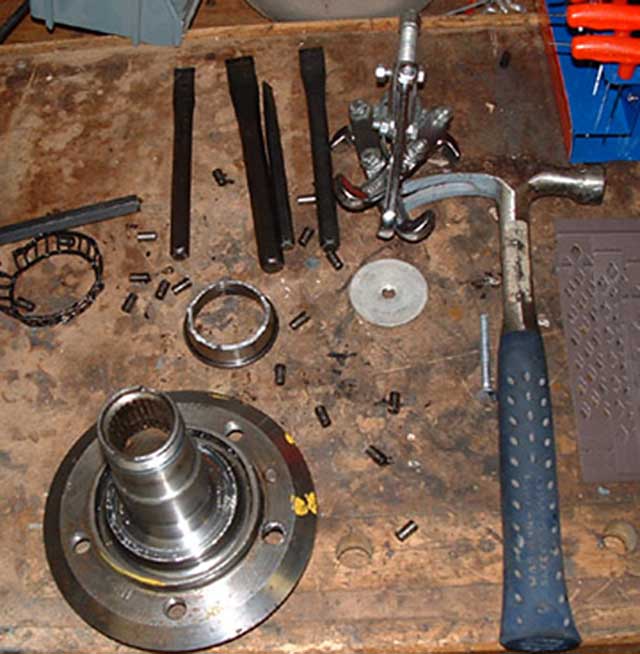
The wheel area needs to be cleaned of all grease and the races removed.
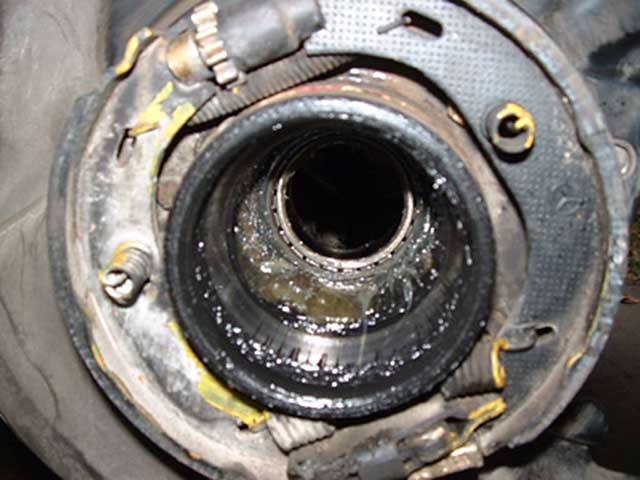
Use a BRASS drift to remove the outside and inside outer races. Using a steel drift will scar the metal and you don’t want that. This picture shows me removing the inside outer race. You remove the outside outer race from under the car
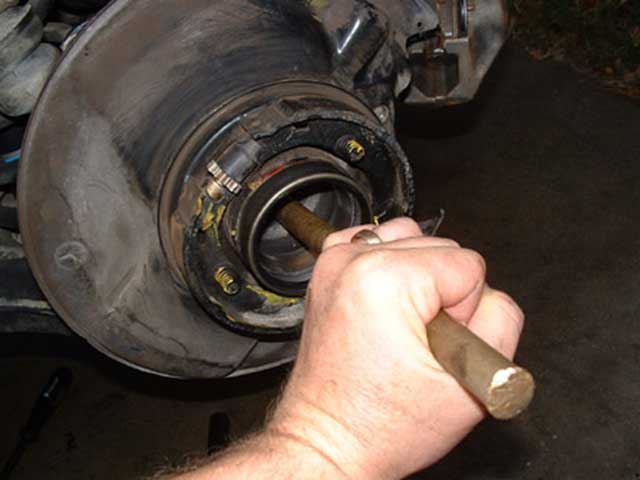
Clean the interior completely of all grease and brass bits that will come off the drift. Use a degreaser, dry it and then blow it out with compressed air.
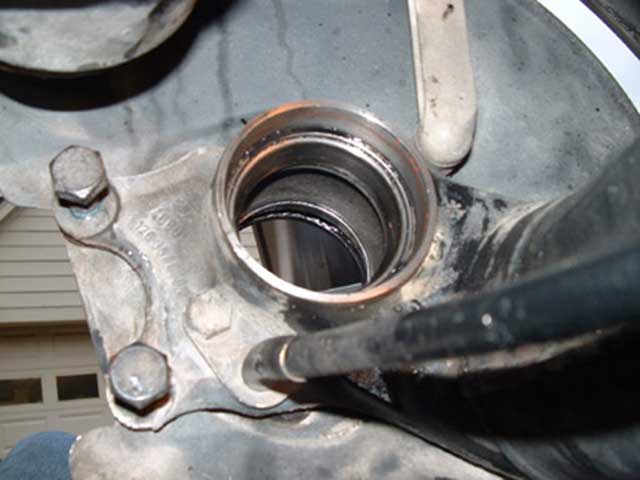
A clean and dry wheel carrier section.
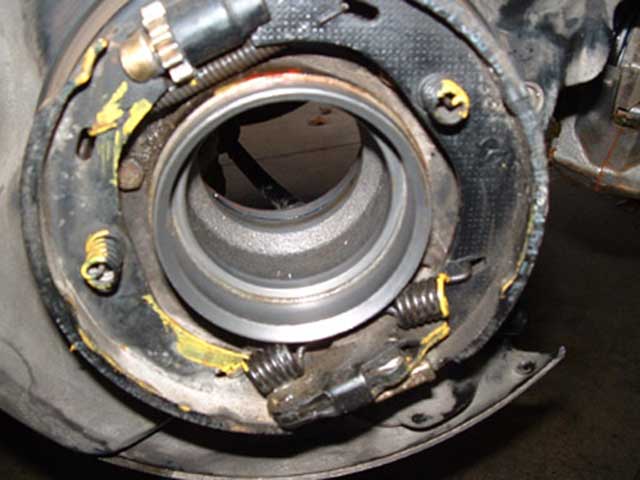
Another view.
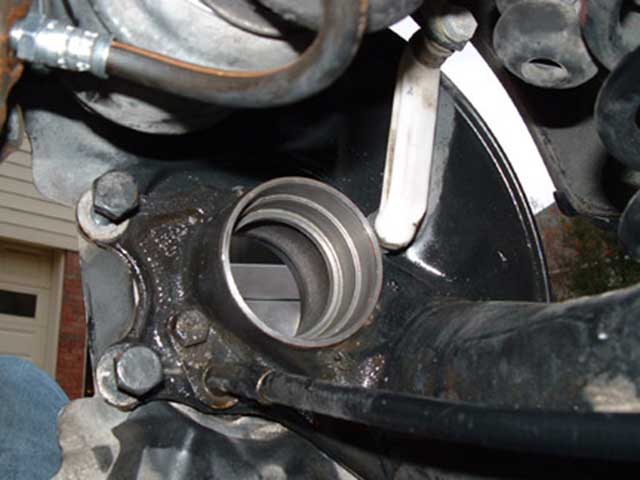
Now install the new races. A technique to use is to use the old race to hit with the hammer as you are installing it. The old race will receive all the blows and the new one will have a solid matting against the old one eliminating damage to the new race. Drive them until they are seated completely.
Pack the bearings with grease first.
Install the new outside bearing on the hub. I used a chisel as shown and ONLY strike the inner race not the bearing cage. Slowly drive it onto the hub until seated. Continuously tap the race rotating all around its circumference.
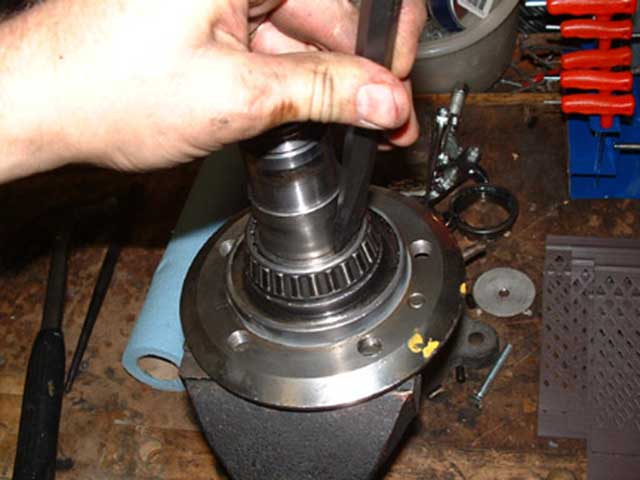
Install grease into the wheel carrier. Total grease installed in the assembly is 50G. This is split between the outside and inside bearings.
Place the crush washer on the hub.
Install the Outer radial seal into the wheel carrier
Install the hub into the wheel carrier.
Grease the inside bearings
To drive the inside bearings into position the MB service manual uses a press. I used the old spacer section and hammered the bearing onto the hub shaft. You will need to hold the hub against the wheel carrier as you hammer. It will not completely set the bearing on the hub shaft. But it allows you to then attach the slotted nut and then tighten the assembly.
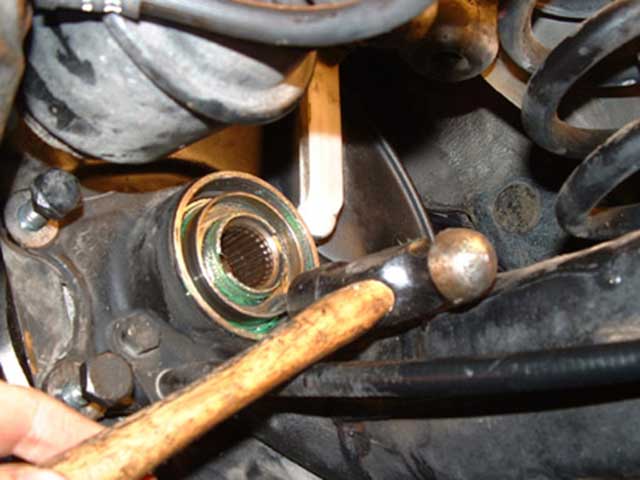
Apply the remainder of the 50G’s of grease as shown..
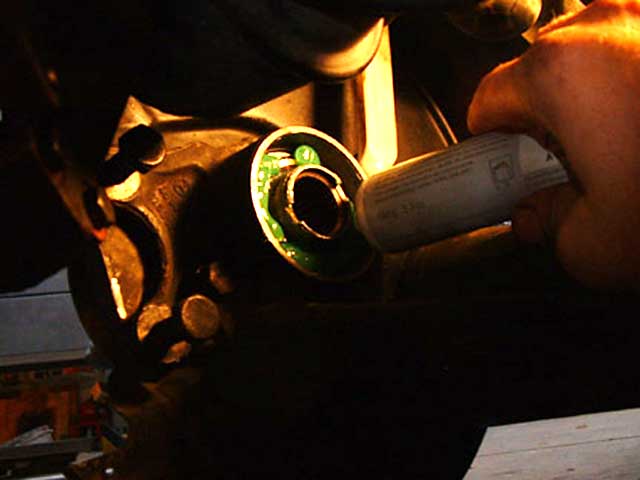
Install the inner radial sealing ring and new inner spacer. I then use a dead blow hammer ( its made out of rubber) and drove the seals into the carrier.
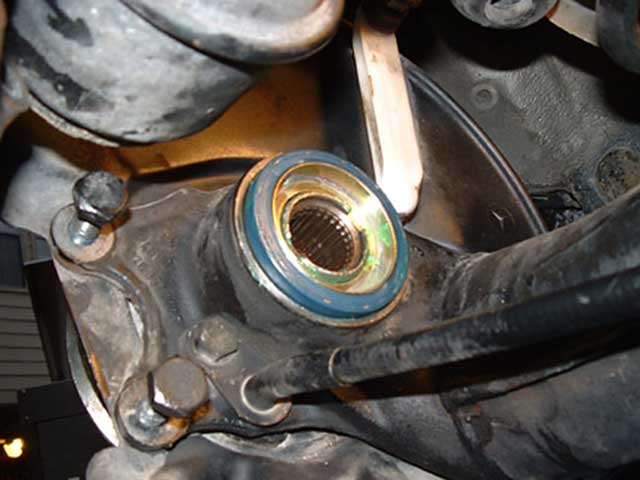
Driving the seals into the carrier.
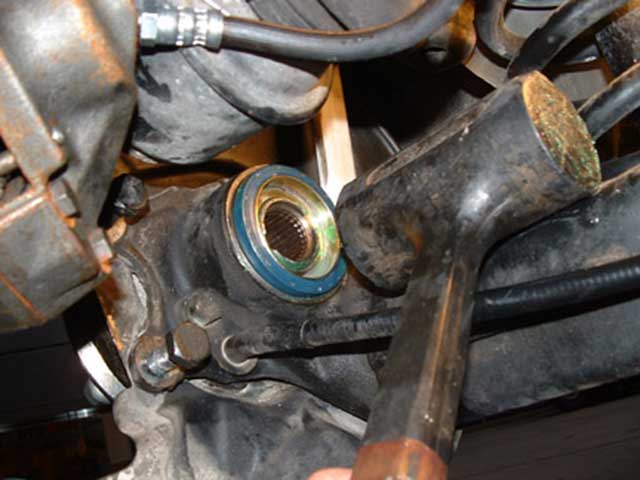
Attach the slotted nut and tighten.
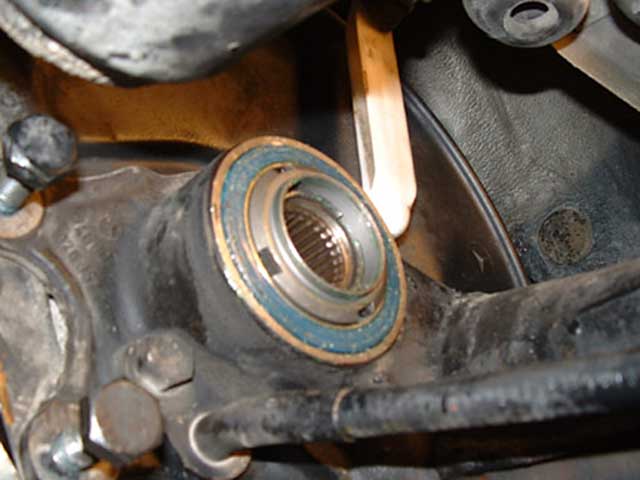
Here the socket is installed and the ratchet attached. I found it necessary to use the dead blow hammer to seat the socket all the way in. I tightened them as much as I could without the black pipe pry bar.
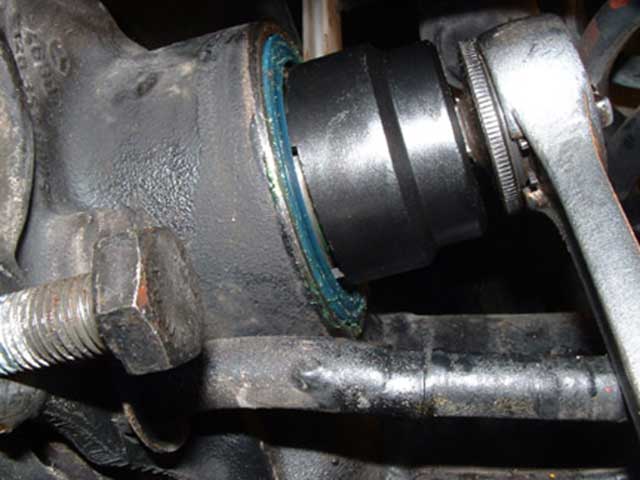
Notes on tightening the assembly.
Hammer the socket into the nut after each tightening of the assembly. THIS IS VERY IMPORTANT or you can break the socket tabs, don’t ask how I know.
Now with the socket installed and the ratchet against the lower control arm. Use the black pipe and the 2 lug bolts to tighten the assembly about 1/8th of a turn.. Measure the tolerance of the hub with a dial set up on a base. Hammer in the socket again and then turn the assembly with the black pipe another 1/8th of a turn. Do this until you have tighten it to within limits.
The limits are 0.04-0.06 mm
SAE .0015-.0023Inch
Or 1 mark on my dial gauge is .001 Inch
If you over tighten the assembly. YOU MUST REMOVE THE CRUSH WASHER AND INSIDE SEAL AND START OVER AGAIN. You will have to buy a new crush washer and inner seal.
This shows the dial gauge tolerance I achieved. One is pushing on the hub and other is pulling on it. I have about a .0015 setting.
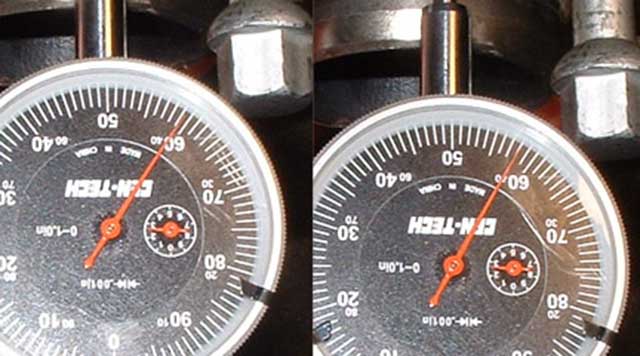
How to set up the dial gauge for your reading.
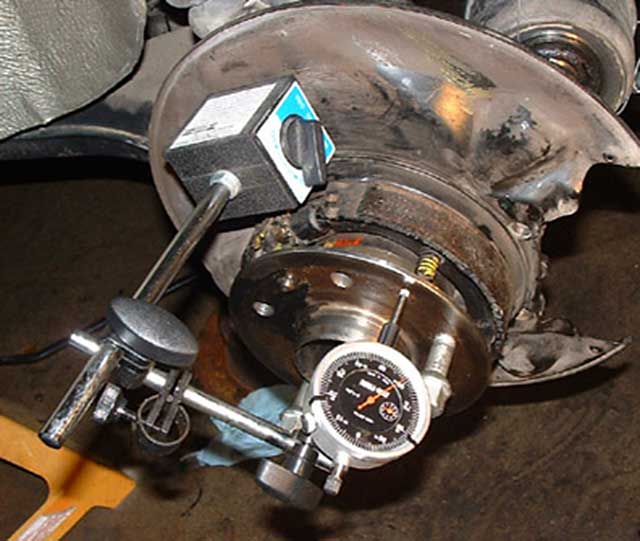
I have the dial gauge and base I bought from Harbor Freight:
Dial
Base
After tightening the hub to tolerance. You "lock" the nut in position by punching the nut flange into the openings in the hub shaft.
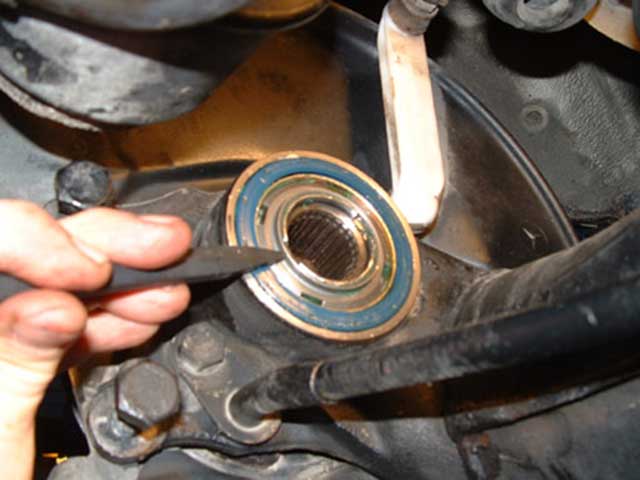
Shows the nut flange punched.
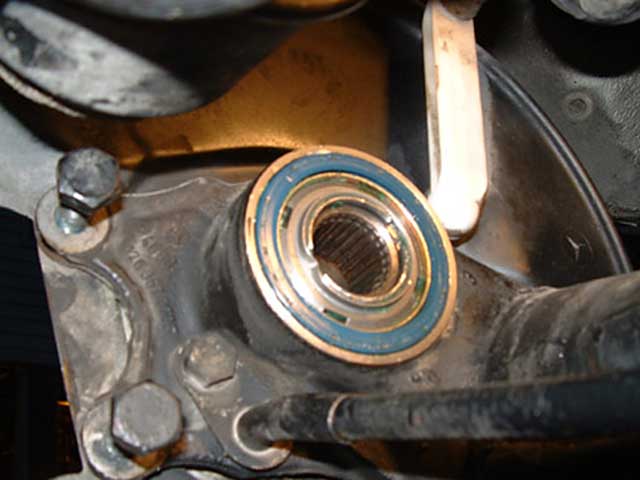
Install the drive axle into the hub and tighten the nut to the specified torque for your type axle. ( M12- 95Nm, M8-30Nm )
Install the rotor on the hub.
Install the calipers over the rotor and bolt onto the wheel carrier using loctite.
Enjoy.
PS - Here is the location to drive the chisel to remove the outer bearing assembly off the hub.
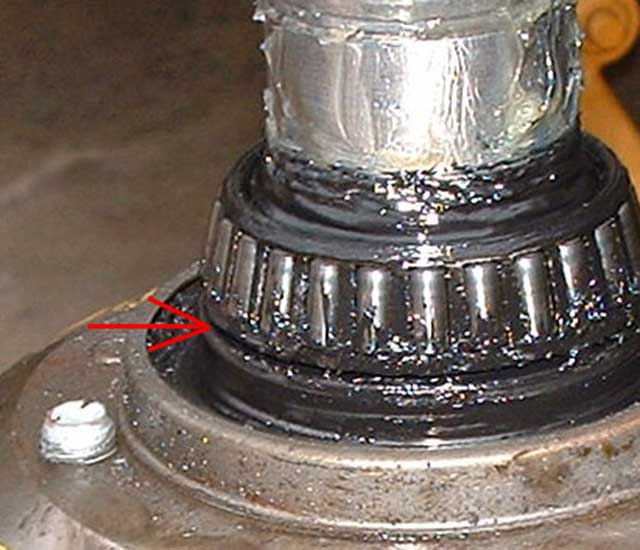
The attached pictures show how I pulled or pushed on the hub so that the movement in and out of the wheel carrier is within the tolerances specified in the Service Manual.
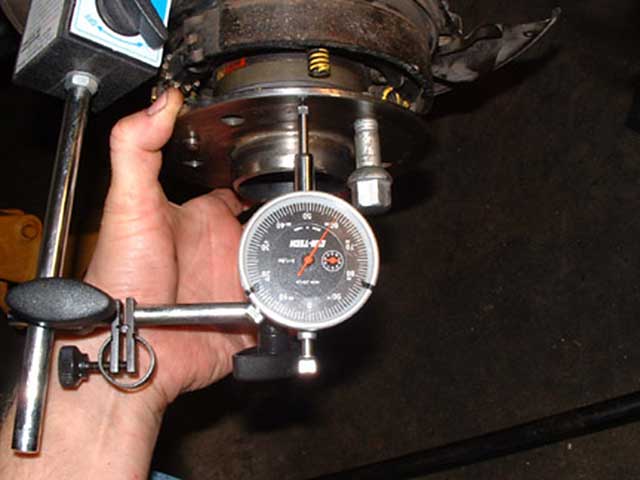
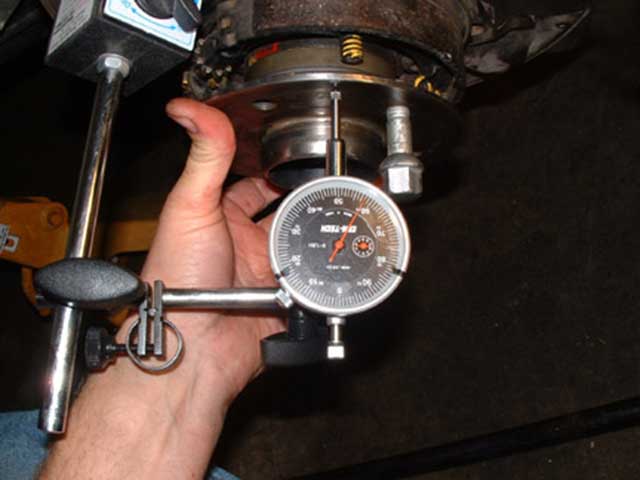
Discuss this DIY here.
-dmorrison
CategoryDiy